
Workers install Uponor
PEX tubing for a radiant heating project at California
Academy of Sciences in San Francisco. Photo
courtesy of Uponor
I began writing about hydronic systems for Supply House Times’ parent company BNP Media about 16 years ago. Back then, each column was created on a boxy little Macintosh computer with a 9-in. screen, printed on a dot matrix printer and saved on a 3.5-in. floppy disk. Every month, a printed copy of the column along with the floppy disk were mailed to the editors. After working their magic, the editors would mail me a copy of the final layout for one last look. If changes were needed, we would work them out over the phone. At the time, this work flow seemed perfectly acceptable. By today’s publishing standards, it seems almost archaic.
Sixteen years ago, hydronic heating was enjoying a resurgence of interest. The market expansion was largely driven by the red-hot topic of radiant floor heating. As the years went on, radiant floor heating continued to be the tail wagging the hydronics dog. During the late 1990s, we became accustomed to radiant heating market growth rates of 25%+ per year. Many aspiring heating professionals were drawn into hydronics through growing interest in radiant heating.
Other hydronic-related topics that generated strong interest during these years included:
- Mixing strategies and devices;
- Protecting boilers against flue gas
condensation;
- Primary/secondary piping;
- Outdoor reset control;
- Radiant-specific thermostats;
- Customized controls using ladder diagrams and programmable logic
controllers;
- Oxygen barrier tubing vs. non-barrier tubing;
- The energy savings of radiantly heated buildings vs. those heated by
other means;
- How comfort was attained at lower air temperatures in radiantly
heated buildings;
- High capacity domestic water heating; and
- Snow-melting: steps, patios, walkways, driveways and entire parking lots.
Conventional fuel was relatively cheap during these times, and the American economy was growing at a healthy rate. These circumstances, in combination with advancing building technology, set the stage for a boom in what many of us now call “McMansion” homes of 10,000+ square feet.
The hydronics industry benefited from these trends and technologies. A growing number of hydronic “artisans” acquired the skills needed to assemble complex hydronic systems that often contained thousands of dollars worth of electronic controls, walls full of circulators and miles of PEX tubing. Many of these residential systems were arguably more complex than systems in much larger commercial buildings. The market was, and still is, awash with devices that allowed these artisans to sculpt increasingly complex and intricate designs. I know, because I was one of them.
Most of these high-end systems worked, but many required several hours of “tweaking” to weed out unexpected control, pumping or balancing issues. I even remember one installer telling me how he “camped out” overnight in mechanical rooms trying to tame some of the beasts he had created.
Some of this is still happening. McMansions are still being constructed, although in fewer numbers. Those that are being built often aspire to be “green” by including renewable energy heat sources. For example, heat may be provided by eight geothermal heat pumps rather than four gas-fired boilers. These systems still involve thousands of individual components that are assembled on site, often under less than ideal conditions.

JAGA’s
ultra-low thermal mass heat emitter with internal microfans is specifically
designed for operation at low water temps. Photo courtesy of JAGA North America
Forced change
The HVAC market got a slap in the face when the bottom fell out of the real estate market in 2007. Double-digit growth gave way to trying to limit losses. Marketing terms such as green, sustainable, renewable and LEED became the industry’s new vocabulary, and inevitably set the trend that has brought us to the present. Today, the topics that consistently generate strong interest in the hydronics industry include:- Solar thermal systems;
- Geothermal, as well as air-to-water heat pump
systems;
- Use of intelligent ECM-based circulators;
- Web-enabled control devices and systems;
- Buffer tanks for correcting boiler
short-cycling;
- Alternatives to PVC appliance venting;
- Small-scale chilled water cooling - both radiant and convective;
and
- Using methods other than primary/secondary piping to achieve hydraulic separation in multiple circulator systems.
Public interest in solar thermal systems and hydronic-based heat pump systems is currently very strong. It’s the result of saturation-level eco-marketing along with government subsidies that generously reward those who use these heat sources. I would venture to say that most of those reading this column, including myself, have seen their businesses affected, hopefully for the better, by this trend.
Appropriate use of renewable energy heat sources is something I strongly support. The fact that hydronics is the underlying technology enabling nearly all thermally based renewable energy heat sources to deliver their energy should be a tremendous “stimulus” for the hydronics industry. However, building a business around currently available government subsidies really worries me. I lived through the early 1980s when the feds first pulled the plug on renewable energy. One lesson I learned was that renewable energy systems will only gain mainstream acceptance when deployed in ways that are reliable, have a long life, are easily repeatable and can create immediate monthly savings without government subsidies. There are some renewable-based systems that meet these requirements and some that fall way outside the reality envelope. Look for the free market to sort them out in the near future.
ECM-based intelligent circulators
If you’ve read my columns over the last few years you know that I’m a big proponent of ECM-based intelligent circulators. I think they represent the single biggest advancement in hydronics technology over the last two decades. I encourage people to think of these circulators as the compact fluorescent light bulbs of our industry. When eventually implemented by the millions, they will have a profound positive effect on our industry. They will also widen the distinction between what’s possible using water-based rather than air-based distribution systems.Primary/secondary piping remains a viable design technique. However, more designers are learning how to use the broader concept of hydraulic separation to provide the benefits of primary/secondary piping without the need of constructing primary loops, or incurring the installation and operating costs of primary loop circulators. Retaining all the benefits while using simpler and less expensive hardware configurations is engineering at its best. Look for this trend to continue.

HTP’s Versa Hydro appliance provides hydronic space heating and domestic
water heating. Photo courtesy of HTP Products
Get in the zone
Zoning has been, and will continue to be a major benefit of using hydronic heating and cooling. However, zoning is steadily shifting from extensive use of small, relatively low-efficiency wet rotor circulators, toward valve-based techniques (e.g., either zone valves or thermostatic radiator valves). There are strong technical and economic arguments to support this transition. This trend will also continue as energy costs increase and more heating professionals learn to market the advantages of these devices.However, yet another approach is just becoming available that will compete with variable-speed circulators combined with valve-based zoning. It’s the use of ultra-low-power fixed-speed circulators, which are now available in North America from at least one supplier. They make it possible to set up typical residential zone circuits powered by individual circulators that, in some cases, can operate on less than 10 watts of electrical input apiece. That’s about 1/8 the power required by a typical PSC-powered wet rotor zone circulator. Either way, it’s apparent that the electrical power used in hydronic distribution circuits can and will be substantially reduced as the industry moves forward.
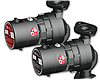
Bell & Gossett’s auto and vario high-efficiency circulators. Photo courtesy
of Bell & Gossett
Some more thoughts
The use of PVC venting for mod/con boilers seems to be at a crossroads. While PVC remains acceptable to some boiler manufacturers, other manufacturers specifically ban its use with their products. The issues in question include long-term integrity of the pipe and its joining methods at higher than expected flue gas temperatures, leaching of potentially corrosive chlorides from the pipe and the lack of specific approvals from some PVC pipe manufacturers regarding use of their pipe for venting heat sources. I think it’s inevitable that polypropylene, and to a lesser degree AL29-4C stainless steel, will become the preferred venting materials for all condensing heat sources.Snow-melting continues to be an option the hydronics industry offers. However, increasing energy prices, growing altruism about reducing energy use and increasingly restrictive energy codes are reducing when and where snow-melting is deployed.
The issue of short-cycling remains a potential Achilles’ heel for those who work with low-mass mod/con boilers. I often ask contractors about this issue and find it to be a pervasive problem. The ability to create a six- or 12-zone system supplied by a low-mass mod/con boiler that can only reduce its output to 20% of full firing rate is the underlying cause of short cycling. This situation wasn’t very common when residential boilers contained 400+ pounds of cast iron, 10 or more gallons of water and served one to three zone distribution systems.
Unfortunately, our industry didn’t appreciate the “self-buffering” characteristics of these older high-mass boilers, at least not until we began using low-mass boilers with ever-increasing numbers of zones. I think the solution lies in restoring thermal mass to the heat source, preferably as site-added water rather than manufacturer-added metal. I predict that future combustion-based hydronic heat sources will increasingly rely on added water content to stabilize their operation in highly zoned systems.
Chilled water cooling has been used in commercial buildings for decades. It’s now poised for increased use in residential buildings for several reasons. One is that radiant cooling systems can shift the sensible portion of the cooling load from air-based distribution to hydronic distribution. With good design, the electrical energy used in the latter is a small fraction of that used in the former. The ability to easily zone hydronic-based cooling vs. air-based cooling is another draw. So is the fact ground-source heat pumps, air-to-water heat pumps and gas-fired absorption heat pumps can all efficiently produce chilled water for cooling, as well as warm water for hydronic heating. Look for ever-increasing interest and application of small-scale chilled water cooling.
Several Web-enabled devices are now available for use in hydronic systems. They include thermostats as well as central controllers used in networked control systems. They enable owners to use a smartphone, tablet or laptop from any place where Internet service is available to monitor or adjust temperatures and operating schedules in their system. They can even send the service technician an email if and when a specific fault condition occurs within the system.
While I remain unconvinced that such devices should be in all new hydronic systems, I respect the fact that wireless mobile Internet access is now a necessity, rather than a frill for many Americans. That being the case, I expect to see increasing availability of Web-enabled devices, even down to components such as circulators, boilers and mixing devices. If it contains a microprocessor, it will likely soon be communicating over the Web.

Wireless
thermostatic radiator valves provide room-by-room temperature control of
baseboard panel radiators. Photo courtesy of Oventrop
The watch list
There are several developing trends that could significantly impact the future growth of our industry. They represent opportunity, if the industry recognizes the need and responds with appropriate solutions. These include:Stay tuned
In the months ahead I’ll be keeping watch on these trends and writing about them for Supply House Times.I’ll write those future columns on an iMac with a 27-in. color LED display, email them to the editors and very seldom print anything. The computer I used to write my first columns has long since evolved into a device that is now indispensable to my business and has undoubtedly improved the quality of my life. That happened because a certain computer manufacturer recognized the need to provide solutions rather than boxes classified by megahertz and gigabytes.
Hydronics technology, working behind the scenes and without the glory of eco-hyped headlines, holds the potential to improve the quality of our lives and reduce our national energy needs. This potential teeters on the ability of our industry to deliver solutions rather than hardware. It’s time to rediscover the inherent advantages of hydronics and embed them within preassembled “appliances” that deliver simple, repeatable installations and reliable long-term performance.